The EPSRC recently awarded a large grant (£1.6m) to Professor Steve Eichhorn in the Bristol Composites Institute for a fellowship on “Realising Functional Cellulosic Bio-based Composites”. Fellowships are schemes that allow academics at all levels to focus on research, to make a difference in a field. This fellowship is slightly different, as it includes Equity, Diversity and Inclusion (ED&I). The technical work of the fellowship will focus on biobased and sustainable composites using cellulose towards functional materials. The ED&I aspect of the work will aim to improve the experiences and inclusion of Black students and staff.
ED&I in Engineering
Recent studies have highlighted that fewer than 1% of UK university professors are Black, with previous research showing that there are only 25 Black female professors in the UK.
“For many years during my career, I had been involved in ED&I work. It dawned on me that as a white male within academia not only was I the norm, but I also possessed a lot of privilege that had enabled my career. I also came to realise that I am also part of the problem, with most decision making and shaping of the culture in universities being directed by people who look like me.
The aim of this fellowship is to de-centre that approach, but to also engage more people of all ethnicities to tackle the problem of a lack ED&I of Black and Black heritage staff and students in STEM”, Professor Eichhorn reflects.
For the last 20 years, Professor Eichhorn has been researching the structure-property relationships of cellulose. His research groups have always been diverse, but he has recently realised that certain aspects could still be improved.
“My group over the years has included a wide range of people, with a very good gender balance, but also diverse ethnic, religious, class and cultural backgrounds. This has been a strength to the work we have produced over the last two decades. However, it is evident that people of Black and Black heritage have not been well represented in my group. This is something I have reflected on. This ED&I fellowship gave me a unique opportunity to address this issue and be part of a process of change.”
Cellulosic Bio-based Composites
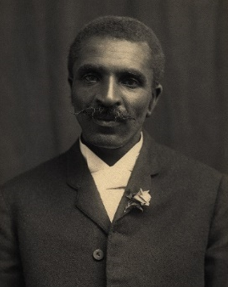
There is a worldwide transition from the use of oil-based to more sustainable materials. This transition is happening due to dwindling oil stocks and a realisation that current levels of the use of this resource are no longer sustainable. However, this is not a new development, as pioneers such as George Washington Carver, working with Henry Ford, developed sustainable and biobased composites in the 1930s. We know from their work that sustainable sources for materials exist in the form of cellulose from plants. This material is a very versatile polymer and is in fact the most utilised material worldwide.
Nature makes use of cellulose to good effect. Being intrinsically strong and stiff means that cellulose fibres, per weight, can compete mechanically with most synthetic alternatives such as glass. In nature’s most prevalent natural composite – wood – cellulose forms the basis of its outstanding structural performance.
All our attempts to replicate the composite performance of wood and plants have fallen short, and this fellowship seeks to address these issues, while also using the intrinsic properties of plant fibres and wood themselves.
Fellowship Research Team
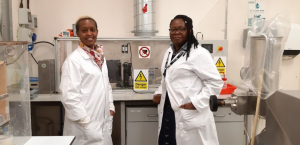
After a search for the right applicants for postdoctoral positions, we were delighted to welcome two researchers – Dr Anita Etale and Dr Amaka Onyianta – with outstanding track records in cellulose research and the lived experience and passion to address ED&I with respect to Black and Black heritage staff and students. They combine these two passions and expertise and are already making an impact in the field.
“I am very glad to be part of this fellowship. This is a rare fellowship that combines my passion for making sustainable materials from nature’s most abundant polymer alongside the opportunity to engage in various ED&I projects that would empower Black and Black heritage staff and students in Bristol and hopefully, the UK at large”, Dr Amaka Onyianta says.
“I believe that representation is key to increasing diversity among the next generation of engineers. Being part of this fellowship gives me the opportunity to play my part in creating a future where ideas are enriched by varied experiences and approaches, and where people have opportunities to pursue the careers they are passionate about, and to contribute solutions to present and future global challenges”, Dr Anita Etale adds.
Find out more
Read more about this fellowship.
For more information, contact Dr Amaka Onyianta, Dr Anita Etale, or Professor Steve Eichhorn.