Koptelov A., Belnoue J.P-H., Georgilas I., Hallett S. R., Ivanov D.S.
The complexity of composites manufacturing stems from the nature of composite precursors—the combination of loosely-joined fibre network and liquid viscous resin—often heterogenous and enhanced with tougheners or functional additives. is compliant, deforms irreversibly, exhibits almost negligible resistance to axial compressive stresses and has a multitude of flow/deformation mechanisms (i.e., the internal or percolation flow of resin, flow of fibrous suspensions, densification of reinforcement, relative movement of plies, and others) – Figure 1. This makes precursors prone to defects at all stages of the composites manufacturing process.
One of the fundamental processes, universal almost for the entire range of composites manufacturing methods, is consolidation, where a composite precursor undergoes compression to engage plies in contact, squeeze out volatiles, control fibre volume fraction and thickness, obtain near-net component shapes, etc. This is a quality-critical process – deformability of composite precursors defines their susceptibility to defects, their compliance with dimensional tolerances, and the occurrence of shape distortions.
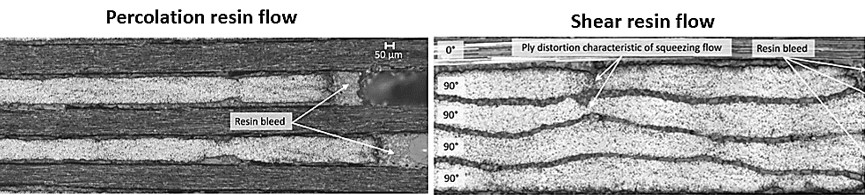
Different forms of deformation mechanisms take place at different structural scales and often occur in parallel. It is essential to have a comprehensive understanding of all these processes to predict the evolution of precursors throughout all stages of composite processing and assess the final architecture/ properties of the composite structure. Each of these mechanisms can be described by material models with various formulations involving large number of material parameters that cannot be determined from direct experiments.
A potentially dangerous trap is that available experimental data are often limited as material testing is both complicated and time consuming. The information obtained in these tests may appear to be deficient and may not reveal all the underlying processes. In this case, property identification may provide a seemingly good fit irrespective of which mechanisms is presumed to happen. However, it does not mean that such model represents the physical reality, and it can often fail to adequately represent a wider set of experimental data. This sets a fundamental dilemma, as the material behaviour (i.e., the model selected) needs to be decided prior to conducting the tests, which introduces a strong subjective element. There is, therefore, a need for a new testing methodology that is capable to identify the deformation mechanisms as well as the relevant material properties. This methodology should be able to check different hypotheses on the deformation mechanisms and autonomously design a testing program based on the measured behaviour of the material.
We have recently developed such adaptive framework [1,2]. It presents a system for autonomous characterisation of materials subjected to an application of pressure and temperature. The system comprises conventional testing machine with heat plates and an integrated “digital brain”, which allows to make decisions on loading path in real time in a “conversation” with material and without human intervention – Figure 2.
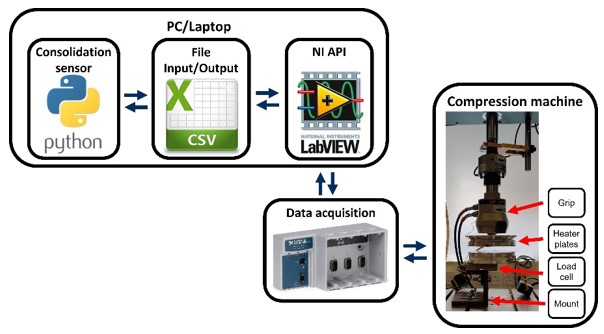
Figure 2. Autonomous testing setup
The framework automatically identifies the characteristic flow processes and the properties associated with the correspondent deformation mode, such as viscosity. As a result of the process, the framework creates a reliable digital twin of the material representative over large range of processing parameters. The fully functioning prototype has been successfully tested for various material systems including toughened prepregs and dry fabrics. These curves are rather different from conventional loading programmes and show the complexity of testing needed to identify the underlying deformation mechanisms.
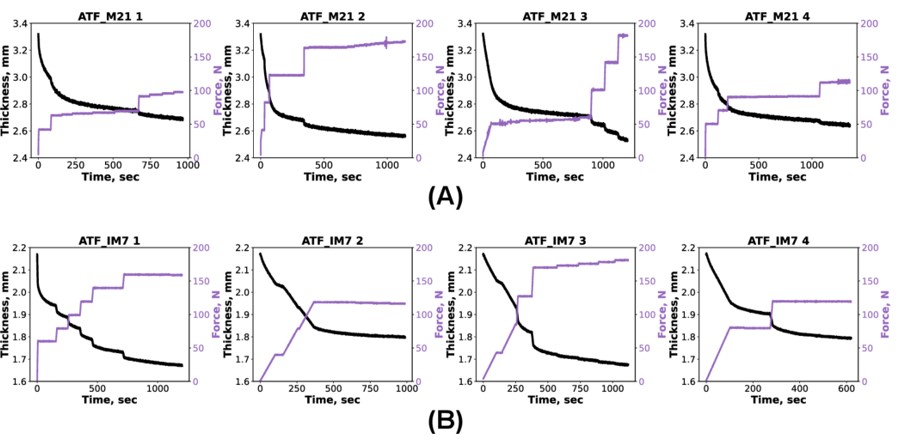
The digitally-driven framework does not just test the material, it defines which flow mode is happening within it and is capable of sensing fine characteristics of material state. The material properties come as a by-product of such examination. This methodology leads to reduced number of experiments while making sure that the obtained data is representative and sufficiently captures all the main features of the material behaviour.
______________
- Koptelov A., Belnoue J.P-H., Georgilas I., Hallett S. R., Ivanov, D.S. Revising testing of composite precursors – a new framework for data capture in complex multi-material systems, Composites Part A, 152 (2022) 106697.
- Koptelov A., Belnoue J.P-H, Georgilas I., Hallett S.R., Ivanov D.S. Adaptive real-time characterisation of composite precursors in manufacturing, Frontiers in Materials, 214.