We interviewed the lead investigator of the SABRE project, Dr. Benjamin Woods.
What is the SABRE project?
SABRE stands for ‘Shape Adaptive Blades for Rotorcraft Efficiency’. The four-year, €6 million, EU-funded project brings together a consortium of six research institutions from across Europe to develop ground-breaking new helicopter blade designs capable of changing shape in real-time to reduce noise, fuel burn and CO2 emissions.
Can you tell us what motivated this work?
In a word, sustainability. Reducing emissions from current flying technology is imperative if we want a credible chance to tackle climate change, hence developing new technologies that are more efficient and drastically reduce fuel burn is key to becoming more sustainable.
How are you proposing to achieve better flying efficiency for helicopters?
Current designs for helicopter blades are rife with inefficiency. The problem with helicopters is that blades will experience cyclic changes in airflow as they rotate. These differences in airflow velocity are detrimental to the performance of the rotor. This is a well-known issue and current rotor designs can change the overall pitch (orientation) of each blade as it spins around the helicopter to partially mitigate this issue. Unfortunately, the pitching solution is not ideal as it pitches the whole blade.
Instead, we are proposing to develop different morphing concepts that will enable us to quickly and accurately control the shape of each blade and hence the airflow, during each rotation.
What are these morphing concepts?
There are many key design parameters that should be considered when creating rotor blades. For example, you should ask ‘how much curvature is there in the aerofoil?’, ‘how does the length of the aerofoils vary over the blade?’, ‘how much twist is there in the blade?’. These are the types of features that engineers play with to optimise rotorcraft performance, with compromises being required due to the wide range of operating conditions. Those are the things that we would love to be able to change – but in real-time – to allow us to fully respond to the different operating conditions without the need to compromise. We are looking at exactly those factors.
Six promising morphing blade concepts are being investigated. Two concepts can actively change the blade twist. Another two can actively change the aerofoil curvature (camber). One concept can increase the length of the aerofoil, and the last concept can alter the blade dynamic response.
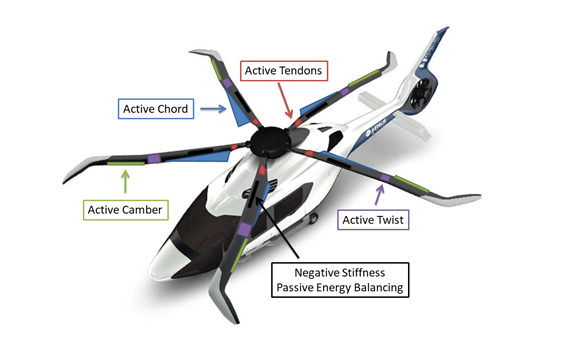
What have you found out so far?
Using one concept at a time resulted in a fuel burn reduction of up to 5%, but when we looked at multiple concepts in different parts of each blade to attack different elements of physics, that’s when we saw significant reductions of up to 11%. There is certainly scope for further reductions, and with the right combination of technologies, fuel burn could be reduced by as much as 20%.
What are your next steps?
It will be a while before this technology becomes mainstream. Development times of up to 30 years are “completely standard” for novel technologies in civil aerospace because the safety requirements are so rigorous. However, SABRE’s research could have applications elsewhere – more specifically, with renewable wind energy. This will likely be part of my next investigation.
Find out more
For more information, visit the SABRE Project website.